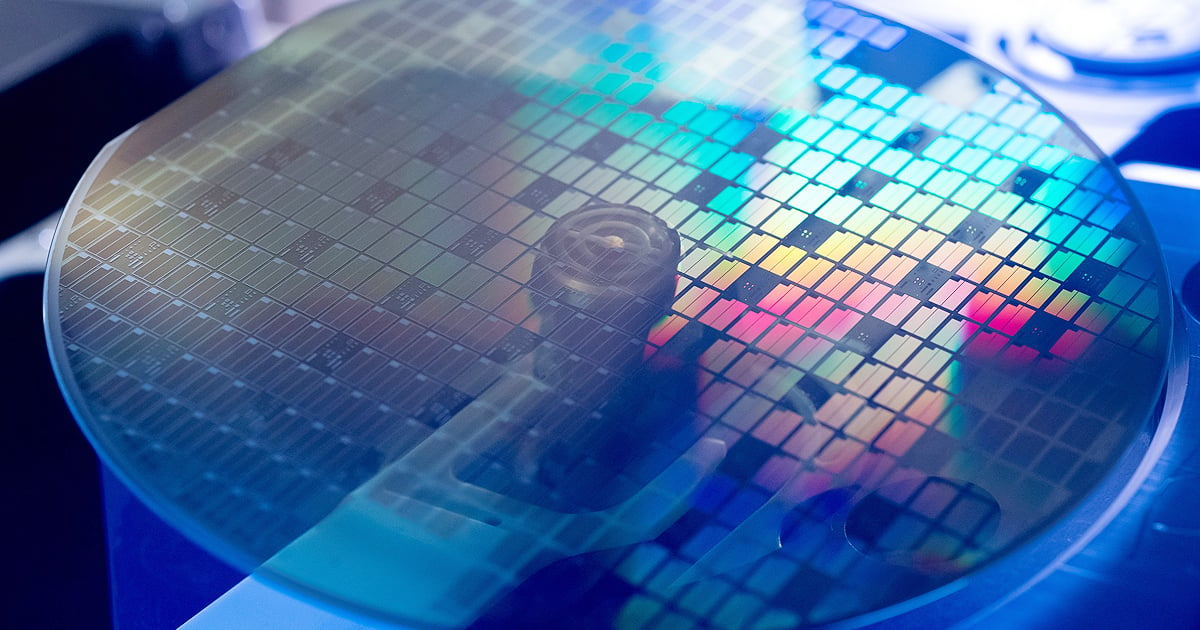
REUTLINGEN, Germany — Suppliers worldwide are investing heavily in silicon carbide microchips to help automakers hit their ambitious electric vehicle targets, spending billions of dollars to secure a stock of them or even make their own.
German supplier giant Robert Bosch is in the midst of a $274.5 million expansion of its semiconductor “wafer fab” here in Reutlingen, Germany, about 25 miles south of Stuttgart. The facility has been a hub for Bosch’s microchip business since the 1970s. But now it is being readied to help the world’s largest supplier make more silicon carbide chips for use in its components.
Like other automotive companies, Bosch sees the market for silicon carbide chips exploding in the coming years, growing by 30 percent annually as vehicle electrification ramps up and automakers shoot for ambitious EV sales and production targets.
“I started in the semiconductor business when [micro-electromechanical systems] were booming,” said Patrick Leinenbach, Bosch senior vice president of semiconductor operations, on a tour of the Reutlingen facility. “It took more than 20 years to see a boom like that again, but that’s what we’re seeing with silicon carbide.”
That surging demand is why the company also moved in April to acquire the chipmaker TSI Semiconductors in Roseville, Calif. Bosch said it will spend $1.5 billion to upgrade the facility to make it a hub for silicon carbide chip production in the U.S. by 2026 as it looks to meet surging demand in the region for components made with the material.
“We are heavily investing in floor space and machines just to be able to fulfill customer demands, which are worldwide because everybody wants to electrify,” Leinenbach said. “And if you want to do that seriously, you have to use silicon carbide chips.”
The material is not new, but it has come into focus for the auto industry over the past several years as manufacturers look for ways to make EVs more efficient and reduce charging times, alleviating two major concerns for many potential EV buyers.
Silicon carbide chips offer many advantages over typical silicon chips when used in EV inverters. They enable faster charging by being more stable at high voltages, take up less room than silicon chips and are more efficient, helping automakers to save space, boost charging times and extend range by as much as 6 percent.
“There’s no way to avoid silicon carbide,” Leinenbach said. “If you want to do power charging, you need silicon carbide. I don’t want to charge an electric car for three hours off the highway. I want a super charger that can do it in 10 to 15 minutes.”
It’s a view echoed by executives at many of Bosch’s competitors, as well as those leading major semiconductor makers worldwide.
“With silicon carbide, compared to silicon, you can improve your efficiency by a significant factor,” BorgWarner CEO Frederic Lissalde told Automotive News Europe.
In November, BorgWarner invested $500 million in the North Carolina chipmaker Wolfspeed Inc. as part of a deal that gives the Michigan supplier access to as much as $650 million in silicon carbide chips annually as it ramps up its EV components.
It’s not the only major supplier to invest in Wolfspeed. German supplier ZF Group and Wolfspeed intend to partner on a $3 billion facility in Germany that the companies say will be the world’s largest producer of silicon carbide chips.
“It is clear to us that the opportunity in silicon carbide technology is generational given the pace of adoption we have experienced over the past few quarters,” Wolfspeed CEO Gregg Lowe said on a call with analysts this year.
But silicon carbide production “can present challenges along the way,” Lowe said, in large part because of the difficulty and expense of creating it synthetically.
Demand is far outpacing supply for the material. Wolfspeed’s crystal growth operation, which the company said is the largest silicon carbide facility in the world, cannot make “enough to support the massive accelerating demand” for the material, Lowe said.
That is a factor in the rush for companies to secure future supply now.
In July, Magna International signed a long-term supply agreement for silicon carbide chips with semiconductor maker Onsemi, of Phoenix. Magna will also spend $40 million for new equipment for Onsemi to use for silicon carbide chip production at facilities in New Hampshire and Czech Republic, helping to “ensure access to future supply,” according to the companies.
That deal came just days after Onsemi expanded a previous deal with BorgWarner worth $1 billion.
In June, Vitesco Technologies signed a $1 billion supply agreement with Japanese microchip manufacturer Rohm Co. that will provide Vitesco with silicon carbide through 2030.
The surge in demand is providing a big boost in business for silicon carbide microchip makers. On a call with analysts to discuss Onsemi’s second-quarter earnings results, CEO Hassane El-Khoury said the company is “on track” to hit $1 billion in annual revenue for the first time. Its silicon carbide business had its first-ever profitable quarter in the period ended June 30, the company said.
As competition for chips heats up, automakers and suppliers will be entering into more agreements to secure a supply, especially after having learned hard lessons about microchip supply during the semiconductor shortage of the last few years. And makers of silicon carbide chips are certain to keep making major investments in their production capabilities.
“We want to secure our supply chain,” Bosch’s Leinenbach said “We’re able to produce our own silicon carbide chips and serve our own internal customers and are able to deliver parts when sometimes competitors aren’t able to buy those parts on the market.”