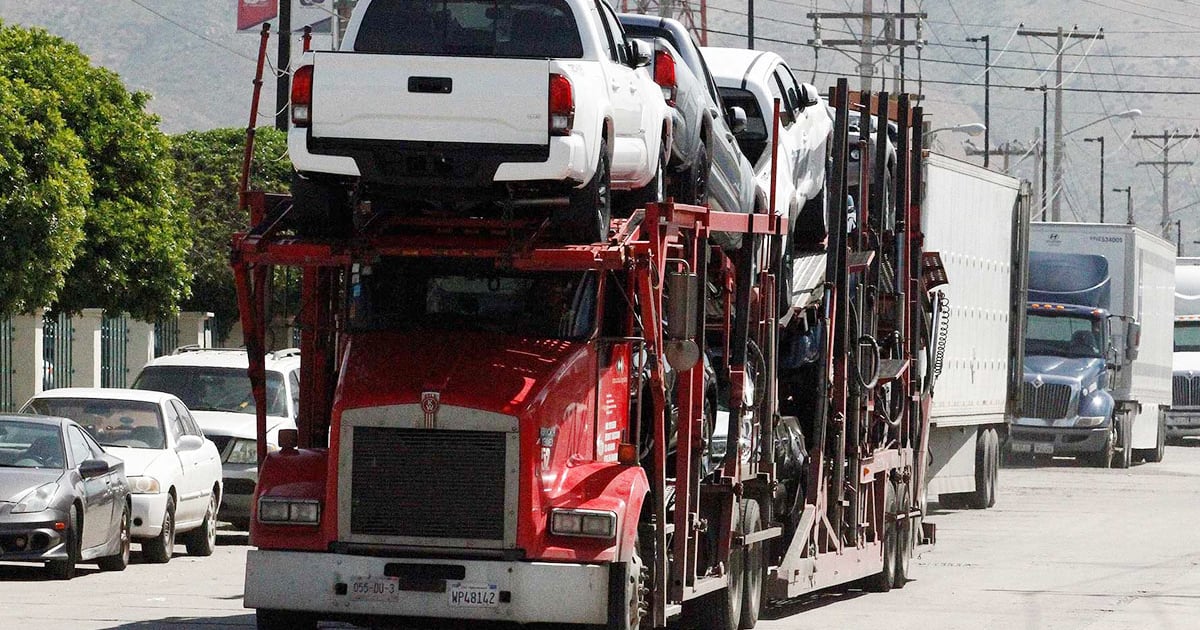
A strike by the UAW against the Detroit 3 could have massive ramifications for logistics and transportation companies that move vehicles and parts throughout the auto supply chain, industry experts said.
“There are entities whose business depends entirely on the movement of automotive parts, and that movement could grind to a halt,” said Laura You, a partner at Warner Norcross + Judd LLP and a member of the Michigan law firm’s automotive and supply chain industry groups.
Some logistics and transportation companies heavily rely on business from the Detroit 3 or the suppliers that build parts for them to stay afloat. A work stoppage at General Motors, Ford and Stellantis could force those companies to lay off workers or pivot to other customers, making it even harder for the automakers and suppliers to ramp production back up when the strike ends.
“When the strike is over, maybe there simply won’t be enough people to move product from point A to point B,” You said.
The UAW’s contracts with the Detroit 3 expire Sept. 14. The industry is bracing for the possibility of a strike that could result in billions of dollars in economic losses if the union and automakers are not able to come to an agreement.
The logistics industry remains in a somewhat fragile state, as evidenced by the Aug. 7 bankruptcy of trucking company Yellow Corp., a once-dominant player that laid off 30,000 workers when it halted operations. A strike would further complicate business for transportation companies and have “significant” effects in the long run, said Thomas Goldsby, a professor at the University of Tennessee’s Global Supply Chain Institute.
“It’s really about the level of dedication companies have to the auto industry,” he said. “Those folks that are dedicated are going to be particularly nervous in the coming weeks.”
Goldsby said companies have attempted to diversify their customer bases over the last several years, as supply chain challenges demonstrated the risks of relying too heavily on a single customer or industry. Others are likely to dedicate more resources to shipping other industries’ goods in the event of a prolonged strike, he said.
“They’ll say, ‘OK, we have warehouse space and trucks in place, so how can we redeploy those assets?’ And they can redeploy them,” he said. “We’re getting close to the peak shipping season for the holidays, and if they’re running tight on inventory for consumer goods, conceivably they could repurpose that space.”
Given those factors and the financial pressures suppliers have dealt with over the past few years, You encouraged parts makers to proactively open lines of communication among their customers, suppliers and logistics companies.
In particular, she said it would be important for suppliers to ask to customers what their ordering plans would be in the event of a strike and to communicate what lead times might be to return to full-volume production after it ends.
“This is not the flip-the-switch sort of industry where suppliers can go from zero to 100 overnight, but that might be the expectation of your customer when the strike ends,” she said. “It’s important [suppliers] set the expectation now for what a production ramp-up looks like in the event that their ordering is completely stopped for the duration of the strike.”
Suppliers should also have a clear idea of what parts are being shipped into their facilities from overseas, a process that could take weeks and leave them storing components for an indefinite period of time, You said.
“The reality of operating in a global industry where the parts you need to produce a component are an ocean away, that means you might’ve ordered parts several weeks ago in compliance with forecasts you received from your customers,” she said. “But once they finally get here in two weeks, you might not have a use for them during the duration of the strike.”
It’s a situation that could by costly to suppliers, since companies don’t get paid for parts until they sell the product it’s used in, she said.
“This is a just-in-time industry, so a lot of facilities have limited capacity for storing inventory,” You said. “Maybe there’s some warehousing you can do off-site, but that costs money to do.”