Nissan is one of several automakers that see solid-state battery technology as a potential game-changer for EVs going into the next decade. In-house, it plans to both perfect development of all-solid-state battery (ASSB) cells and establish how to make them, with the tech due to make it into a production EV by 2028.
If all goes well, Nissan wants to lean on the tech so more vehicle types—especially SUVs, pickups, and vans—make sense in fully electric form by the end of the decade.
That appeared to be the gist behind the Hyper Tourer concept Nissan displayed at the Tokyo auto show last week, suggesting a very thin, flat solid-state battery pack below the floor, affording long-range cruising without the packaging compromise.
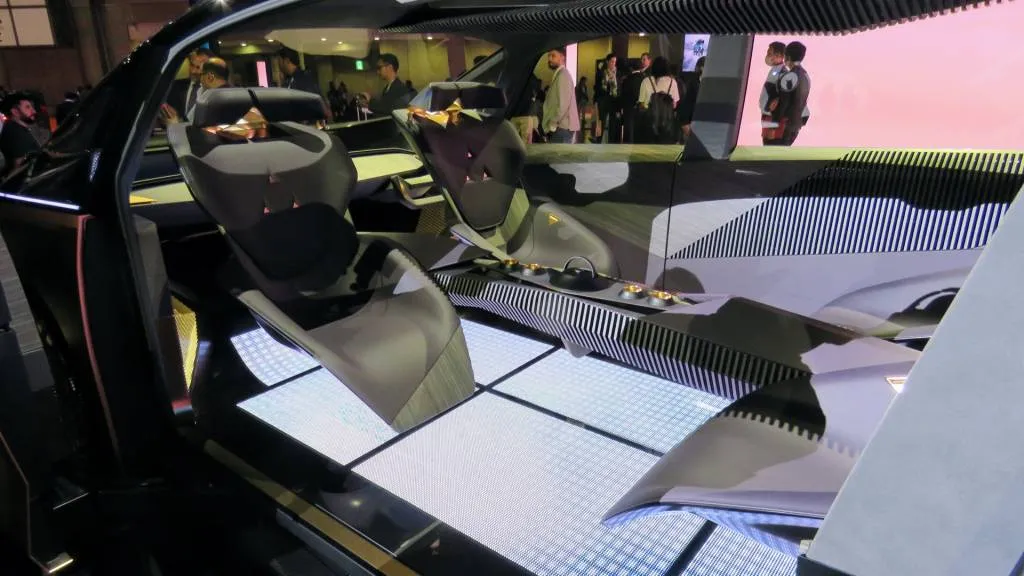
Nissan Hyper Tourer concept
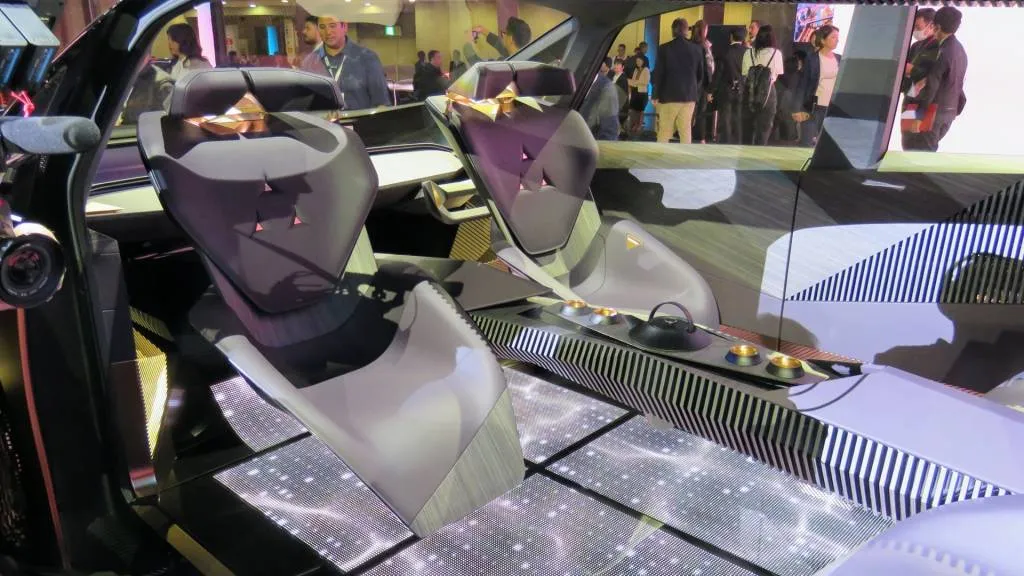
Nissan Hyper Tourer concept
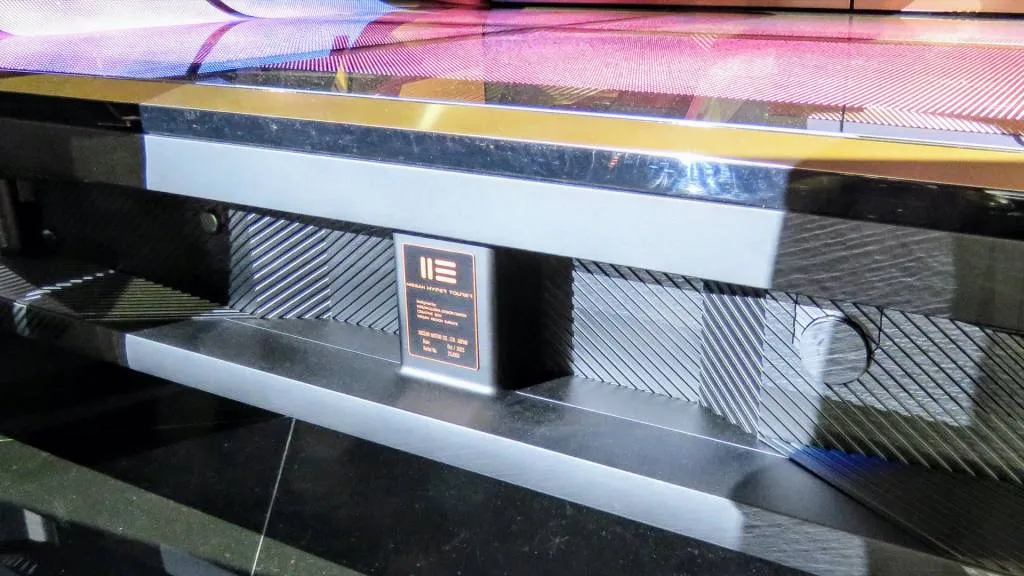
Nissan Hyper Tourer concept
Versus the current lithium-ion cell tech in EVs, Nissan is aiming to effectively double the energy density at the pack level, while cutting the fast charging time by two-thirds.
At the same time, lithium-ion chemistries and other battery types are evolving and improving. In a roundtable interview last week at the Tokyo auto show, Nissan’s global R&D chief Kazuhiro Doi told Green Car Reports that solid-state cell tech can’t just be an incremental improvement over lithium-ion.
To hit those goals, Doi underscored, it will ideally need to go with no cooling at all.
Solid-state runs hot and that’s OK
“In the case of ASSB, maybe we can eliminate the cooling,” he said, emphasizing that it’s still not fixed on a final design, but it’s aiming to avoid it entirely.
As Doi confirmed to some raised eyebrows and verified to Green Car Reports, that means no water cooling, no forced-air cooling, and not even any passive cooling—certainly different than what some automakers have suggested.
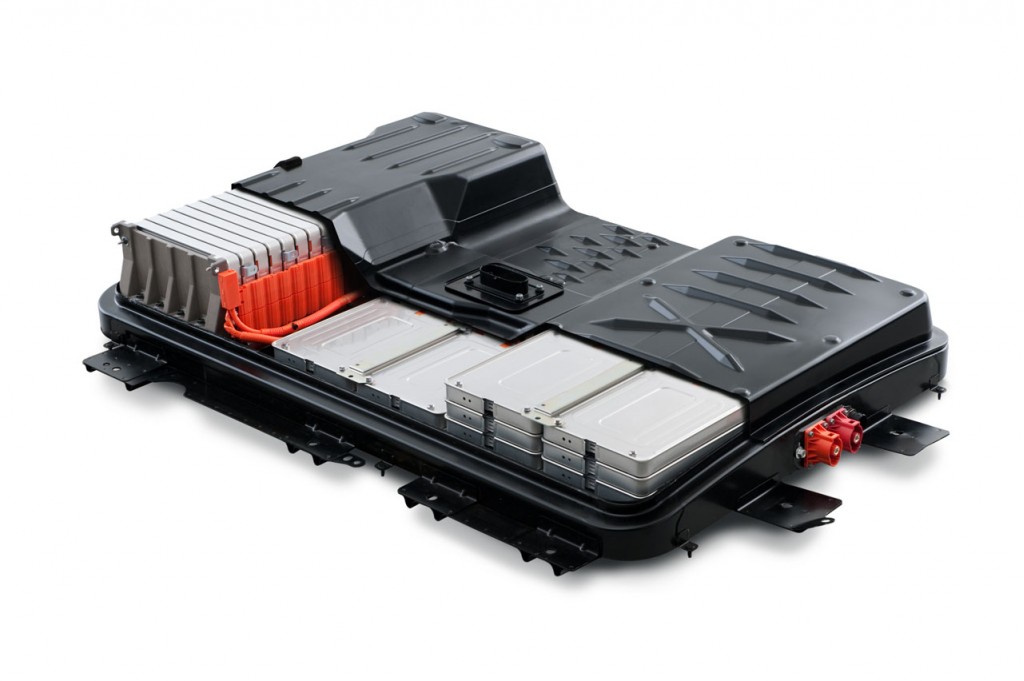
2011 Nissan Leaf – battery pack cutaway
It is a bit of a loaded subject. Nissan underestimated the cooling needs of the original battery cells used in the Nissan Leaf, which degraded quickly in hot climates when parked over hot blacktop or fast-charged too frequently. A subsequent battery-chemistry change in 2015 helped solve that, and since then Leaf battery degradation has been much better.
Getting rid of the bulky water-cooling system in other modern EVs has been a goal for development engineers. Mercedes considered air-cooling in its recent EQXX concept, presaging its new generation of EVs—still with lithium-ion cells—and ultimately decided against it.
But Nissan has more hands-on experience with the tech already, and the rationale behind going without cooling for ASSB is simple: It’s OK for them to get much hotter than what would be considered normal for other EV batteries, and the cells have a wide temperature sweet spot—from room temperature all the way up to 100 degrees C or 212 degrees F.
To maintain the advantage over lithium-ion chemistries and make all the development worthwhile, Nissan will need to have a superior product by then that wouldn’t be dependent on cooling, Doi again emphasized.
For most lithium-ion cells, the temperature threshold is about 60 C or 140 F, and fast charging times are limited to prevent cell temperatures from approaching that temperature. Without worrying so much about temperature, Nissan’s solid-state cells might be able to charge to near 100% in about 15 minutes.
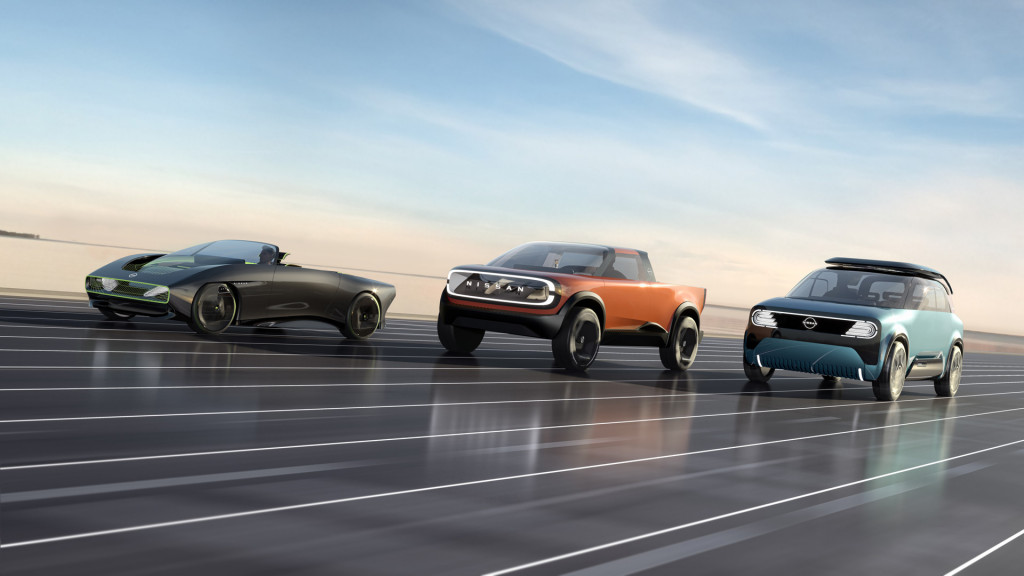
Nissan Surf-Out, Max-Out and Hang-Out concepts
Nissan sees solid-state going big first
Solid state could be applicable to all types of vehicles. While some companies—Toyota, for instance—have hinted that solid-state cells might first appear in hybrids. Nissan believes one type of model makes more sense to take solid-state first: big, long-range, fully electric vehicles.
Doi explained that trucks, vans, and SUVs require much more energy, “but if we utilize that today with lithium-ion battery tech, the size is huge.” Cutting the cooling system out of the equation would mean smaller packaging and far less complexity for the battery pack, allowing it to free up space for roomier vehicles—or, potentially, for more range and less mass.
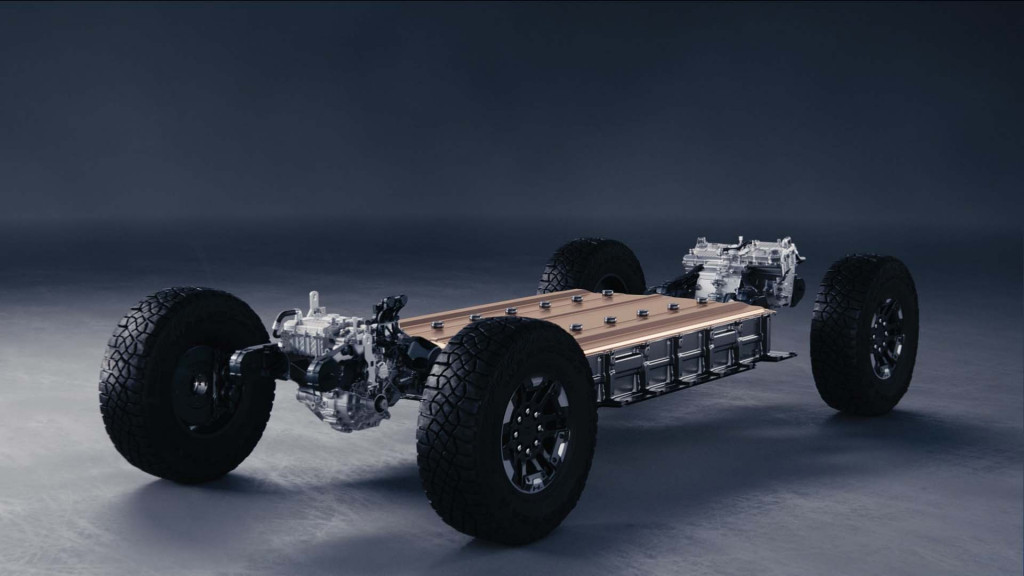
2022 GMC Hummer EV
Juggling power, safety, cycle life
This time around, Nissan needs to get the battery composition right from the start, and there are longevity hurdles yet to solve. In a laboratory situation with scaled-up test cells it’s seeing around 200 cycles—not anywhere near enough for a production EV yet.
After first working with single-layer cells just 2 cm across in the laboratory, Nissan still plans to establish a pilot line for cells about 10 cm across in 2024. The actual production cell will be “much larger” than that, Doi said. Nissan plans to make larger-format cells at the pilot facility, as it works out the size of the plant it might need to ramp up production.
As Doi had previously said, Nissan is incorporating its own nail-piercing tests and X-ray imaging into its studies of the solid-state cells, which will be subjected to rigorous safety and durability testing. The Nissan Leaf has had no instances of fires or thermal runaway, and it’s building these new cells with the same safety priorities.

Nissan solid-state battery prototype production
Nissan’s solid-state tech benefits from a partnership with NASA and UC San Diego in which AI techniques helped choose the best interlayer to prevent the growth of lithium dendrites that might eventually piece through, short-circuiting the cells. The high-ion-conductive electrolyte was chosen for stability, with the anode for high-power potential.
But it’s not done fine-tuning the cells and isn’t able to give specs for them quite yet. Cell performance is not only fixed by chemistry but by the cathode and anode layers, Doi explained. A thicker cathode will yield more energy density but also get in the way of charge rates. “First we need to fix the chemistry, and once we fix the chemistry we can estimate the performance per cell,” he said.
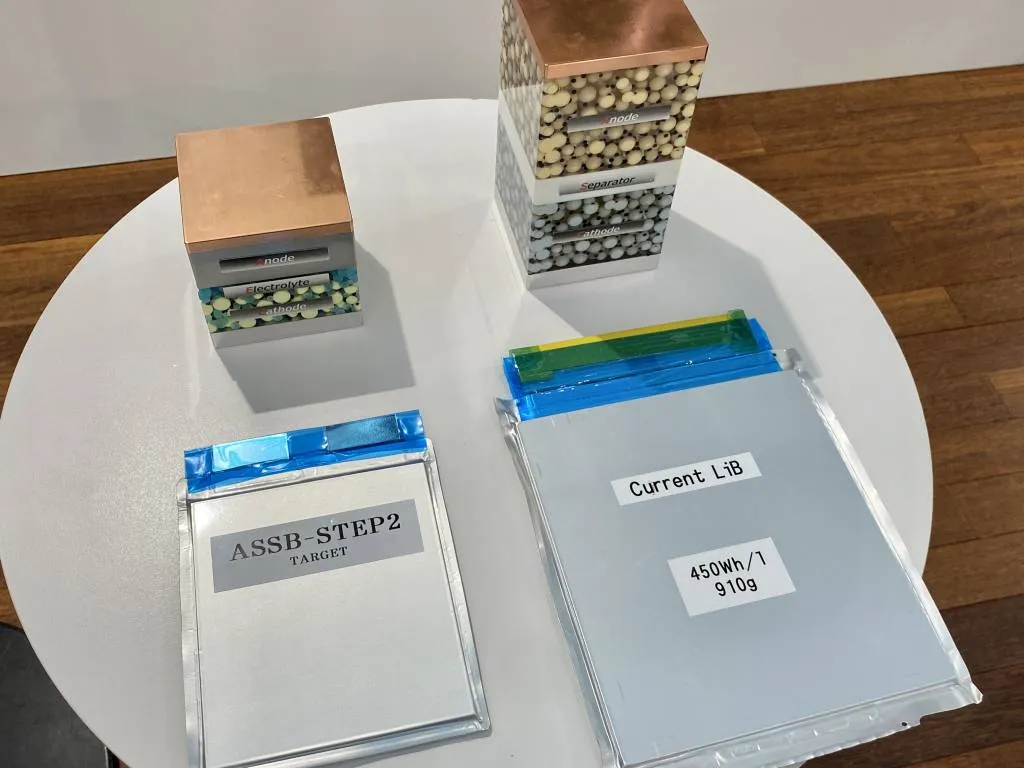
Nissan ASSB vs lithium-ion
Solid-state tech evolution
Doi also emphasized that there will be plenty of evolution of the chemistry. The addition of nickel for energy density and range in lithium-ion cells is one example, he said, and the same sort of thing will happen for solid state.
ASSB aside, high-manganese and sulfur-based chemistries are the next best hope, Doi says. “Then we can utilize that even for the small cars—I think the potential is very attractive,” he said.
Nissan is targeting a cost of just $75 per kwh for solid-state cells, which might put it on par with lithium-ion at the end of the decade. If it can use ASSB for bigger vehicles, the sweet spot for smaller EVs might be in some combination of those chemistries with solid state—an even lower-cost, less-resource-intensive solution without the life-cycle challenges. Cooling for such a combination is yet to be determined, though.