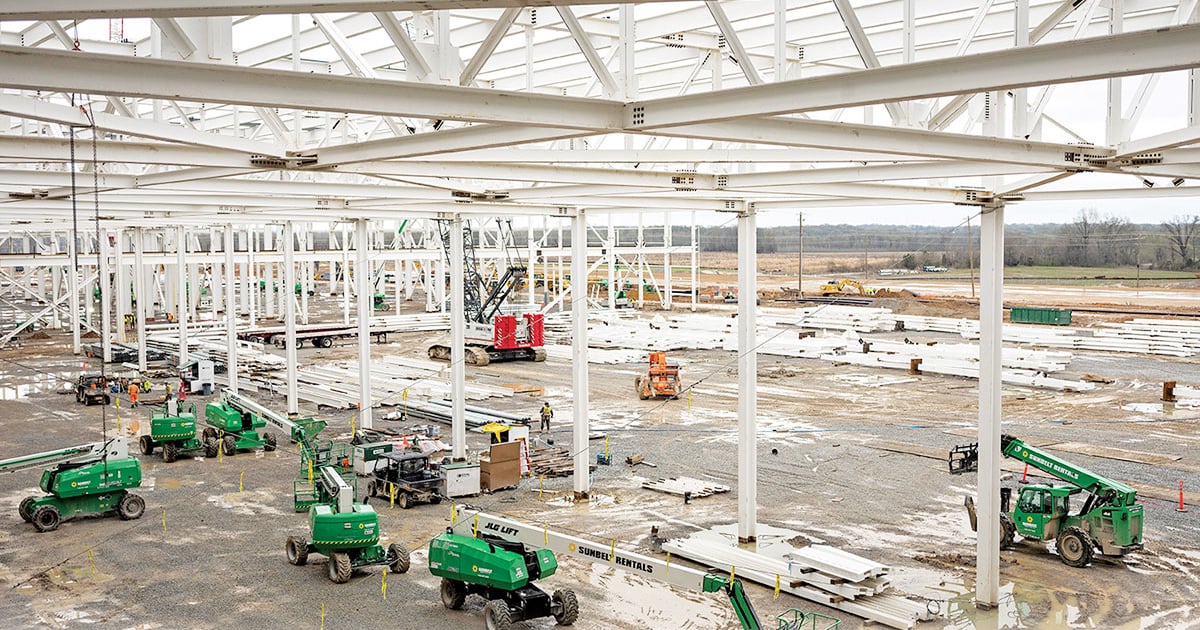
STANTON, Tenn. — At 3,600 acres, Ford Motor Co.’s BlueOval City manufacturing campus here will dwarf even the sprawling Rouge Complex in Michigan.
The centerpiece of the site, a 4-million-square-foot assembly plant that will produce a next-generation electric pickup, will be the largest Ford has ever built. But it could have been even bigger.
Ford said the $5.6 billion project, expected to come online in 2025 with an annual capacity of 500,000 electric vehicles, will have a 30 percent smaller footprint than other plants with similar capacity. That’s because the company, for the first time in recent memory, is designing both a plant and its product simultaneously, and is building in efficiencies that don’t exist at other sites.
“When you walk in, it will not feel like a plant that you’ve been in before,” Lisa Drake, Ford’s vice president of EV industrialization, told Automotive News. “Our target was to actually build this truck more efficiently than the best truck we build — and we build trucks pretty well.”
The plant will have fewer workstations, Drake said, and the vehicle built there, known internally as Project T3, will be offered to customers in significantly fewer configurations than today’s models.
“It’s a marvel of simplification,” CEO Jim Farley said at an event here in March.
Farley has stressed a need to reduce complexity and eliminate waste throughout Ford’s operations, saying the company must cut the number of fasteners in its vehicles by half and move to larger casting with fewer parts, like Tesla does, to achieve its goal of 8 percent margins on EVs.
“It’s more radical than just fasteners and brackets,” Drake said. “We’ve done some systems engineering work where, essentially, we’ve taken pieces of the truck and reduced the design content down so it’s a much more reductive design with less tooling and less people needed to install.”
Still, Ford expects to employ 6,000 workers at the site.
Ford has said BlueOval City will be three times larger than the Rouge. The Dearborn Truck Plant within the Rouge is 1,100 acres and employs 4,500 workers. The Rouge Electric Vehicle Center is 12 acres and employs 750.
Beyond the assembly area, Drake said the paint shop, often the most expensive part of a plant, also will be smaller. She said the company is building it “more vertical than horizontal” and that it will contain some Ford-exclusive technologies, although she declined to provide further detail.
Farley said Ford is applying what it has learned from the Mustang Mach-E and F-150 Lightning EVs, which are currently unprofitable, to the BlueOval City truck, which is expected to be the first vehicle on Ford’s dedicated battery platform.
“The most important thing is to reduce the labor content,” Farley said. “We’re insourcing with batteries and things like that. The vehicle’s designed in such a way — because it’s second-generation — where we radically simplified the subassemblies. It’s a really big change, the way this will be built.”
BlueOval City will be Ford’s first carbon-neutral site and the assembly process will use no fresh water. It will use geothermal, solar and wind power, officials have said.
The campus will have its own utility system, which Ford said will save 50 million gallons of water each year by reducing evaporation from the site’s cooling towers.
Ford is planning a stormwater management system to protect the environment and will leave 380 acres for farming until that land is needed for future expansion.
“This will be a seminal moment like the Rouge was, but this is a new industrial revolution about clean, carbon-neutral manufacturing,” Farley said. And, just as the Rouge pioneered aspects of vertical integration, Ford intends to do the same at BlueOval City.
The campus also will have a battery plant operated by Ford and partner SK Innovation. There, Ford said, workers will build battery cells and arrays, assemble battery packs and deliver the finished product to the assembly plant in less than 30 minutes.
An on-site supplier park will include battery recycling company Redwood Materials. An upfit center is also planned that can add accessories before the trucks are shipped to dealers.
“We’re going back to how Henry Ford set up the assembly line,” Farley said. “We’re going to do more of this ourselves.”