A ramjet engine utilizing rotating detonation combustion could offer major efficiencies for future high-speed air vehicle designs.
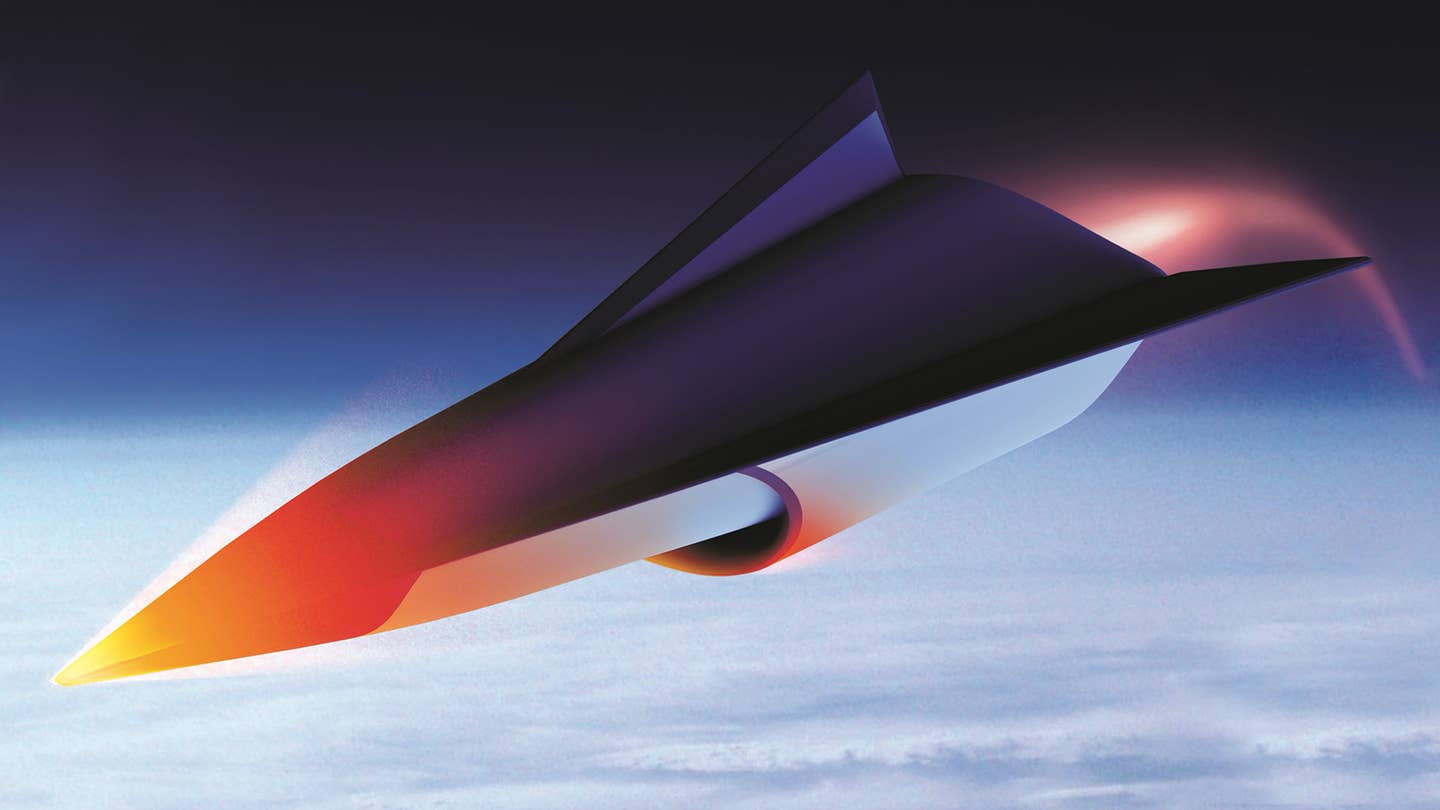
GE Aerospace says it successfully demonstrated an advanced jet propulsion concept that involves a dual-mode ramjet design utilizing rotating detonation combustion. This could offer a pathway to the development of new aircraft and missiles capable of flying efficiently at high supersonic and even hypersonic speeds across long distances.
A press release that GE Aerospace put out today offers new details about what it says “is believed to be a world-first hypersonic dual-mode ramjet (DMRJ) rig test with rotating detonation combustion (RDC) in a supersonic flow stream.” Hypersonic speed is defined as anything above Mach 5. Amy Gowder, President and CEO of the Defense & Systems division of GE Aerospace, previously disclosed this project, but offered more limited information, at this year’s Paris Air Show in June.
A rendering of a rotating detonation engine design. USAF/AFRL via Aviation Week
“A typical air-breathing DMRJ propulsion system can only begin operating when the vehicle achieves supersonic speeds of greater than Mach 3,” the press release explains. “GE Aerospace engineers are working on a rotating detonation-enabled dual mode ramjet that is capable of operating at lower Mach numbers, enabling the flight vehicle to operate more efficiently and achieve longer range.”
“RDC [rotating detonation combustion] enables higher thrust generation more efficiently, at an overall smaller engine size and weight, by combusting the fuel through detonation waves instead of a standard combustion system that powers traditional jet engines today,” the press release adds.
To elaborate, in most traditional gas turbines, including turbofan and turbojet engines, air is fed in from an inlet and compressed, and then is mixed with fuel and burned via deflagration (where combustion occurs at a subsonic rate) in a combustion chamber. This process creates the continuous flow of hot, high-pressure air needed to make the whole system run.
A rotating detonation engine (which involves combustion that happens at a supersonic rate) instead “starts with one cylinder inside another larger one, with a gap between them and some small holes or slits through which a detonation fuel mix can be pushed,” according to a past article on the general concept from New Atlas. “Some form of ignition creates a detonation in that annular gap, which creates gases that are pushed out one end of the ring-shaped channel to produce thrust in the opposite direction. It also creates a shockwave that propagates around the channel at around five times the speed of sound, and that shockwave can be used to ignite more detonations in a self-sustaining, rotating pattern if fuel is added in the right spots at the right times.”
The video below offers a more detailed walkthrough of the rotating detonation engine concept.
Experimentation with rotating detonation concepts dates back to the 1950s, but actually creating a workable engine of this type had proved elusive until very recently, at least publicly. In 2020, a team at the University of Central Florida (UCF), working together with the U.S. Air Force’s Air Force Research Laboratory (AFRL), said they had created a first-of-its-kind experimental test rig that demonstrated the concept’s practical feasibility. The following year, the researchers at UCF announced they had built a prototype engine capable of producing a sustained detonation wave, said to be another world’s first. There have been additional developments with regard to rotating detonation engines elsewhere in the United States and around the world since then.
Pictures of the University of Central Florida’s (UCF) rotating detonation test rig that were released in 2020. UCF
In principle, rotating detonation requires less fuel to produce the same level of power/thrust as combustion via deflagration. The resulting sustained shockwave builds its own pressure, as well, leading to even greater fuel efficiency. Pressure is steadily lost during deflagration.
In addition, rotating detonation typically requires far fewer moving parts than are needed in traditional gas turbines. In theory, this should all allow for rotating detonation engine designs that are significantly smaller, lighter, and less complex than existing types with similar very high power/thrust output.
The potential benefits of such a propulsion system are obvious. A practical rotating detonation engine would offer a way to get higher performance and greater range out of even relatively small aircraft and missile designs. Adapting existing designs to use this kind of propulsion could free up space for more fuel or other payloads. These are all potential benefits that AFRL has very publicly touted in the past, as can be seen in the video below.
Last year, the U.S. military’s Defense Advanced Research Projects Agency (DARPA) unveiled a project called Gambit, which is also centered around rotating detonation engine technology. The core goal of this effort is “to develop and demonstrate a novel Rotating Detonation Engine propulsion system that enables a mass-producible, low-cost, high-supersonic, long-range weapon for air-to-ground strike in an anti-access/area denial (A2AD) environment.”
Artwork the Defense Advanced Research Projects Agency (DARPA) has previously released related to the Gambit project. DARPA
In October of this year, Raytheon secured a contract from DARPA to develop and demonstrate a practical rotating detonation engine for the Gambit project.
“Although GE was not selected for the recently revealed DARPA-funded Gambit program—an effort intended to provide a long-range strike missile for fourth-generation fighters leveraging RDE technology—Gowder said, ‘We’re working with them on some other technology demonstrators.'” Aviation Week reported earlier this year around the Paris Airshow.
A rendering of a notional rotating detonation engine-powered missile that the Air Force Research Laboratory (AFRL) has previously released. USAF/AFRL via Aviation Week
The propulsion concept that GE Aerospace says it is now working looks to go a step beyond the basic rotating detonation concept and the benefits that it might offer by blending it together with a dual-mode ramjet design. Ramjets, which are not new, don’t work at subsonic speeds and have trouble working reliably even at lower supersonic speeds. As such, platforms that utilize them require some kind of initial boost, typically provided by a rocket motor.
“GE engineers are now testing the transition mode at high-supersonic speeds as thrust transitions from the RDE-equipped turbine and the dual-mode ramjet/scramjet,” GE Aerospace’s Gowder said in Paris earlier this year, according to Aviation Week.
“We’re looking at both,” Gowder added when asked about her company’s continued work on scramjets. “But the RDE offers a very efficient solution because it allows you to shrink the length. Size, in certain applications, could really matter—particularly for some unmanned applications.”
A combined ramjet and rotating detonation concept could be an especially big deal for future missiles, like the ones DARPA’s Gambit project is envisioning, and possibly high-speed air vehicles for reconnaissance use. This propulsion arrangement could allow for greater efficiency and lighter (and potentially smaller) airframes, which in turn allow for greater performance — especially in terms of range — and/or payload capacity. If rotating detonation combustion can reduce the minimum speed required to get the ramjet working, this would reduce the amount of initial boost such a system would need at the outset, too. This would mean a smaller overall package. All of this opens doors to new levels of operational flexibility.
This new engine concept could also potentially become one component of what is known as a turbine-based combined cycle (TBCC) engine arrangement, of which much talk over the years about in recent years. Most TBCC design concepts revolve around combinations of advanced ramjets or scramjets for use at high speeds and traditional turbojet engines that work better a low speeds.
A graphical depiction of a notional turbine-based combined cycle engine arrangement. Lockheed Martin
A practical TBCC concept of any kind has long been a holy grail technology when it comes to designing very high-speed aircraft. A propulsion system that allows for this kind of high and low-speed flexibility would mean an aircraft could take off from and land on any suitable existing runway, but also be capable of sustained high-supersonic or even hypersonic speeds in the middle portion of a flight.
The U.S. Air Force, among others, is therefore unsurprisingly interested in TBCC propulsion systems. The service’s shadowy Mayhem program has been tied to TBCC and dual-mode ramjet developments in the past, as has Lockheed Martin’s previously proposed SR-72 hypersonic aircraft. Mayhem itself is ostensibly centered on the development of an experimental hypersonic air vehicle capable of carrying various payloads necessary to conduct strike and intelligence, surveillance, and reconnaissance missions.
A rendering of a notional hypersonic air vehicle from Leidos, which is currently leading work on the Air Force’s Mayhem project. Leidos
For the U.S. military, future aircraft and missiles capable just of more efficient sustained supersonic speed over long distances could be very valuable for responding to a variety of time-sensitive mission requirements. In particular, any future high-end conflict in the Pacific, such as one against China, would automatically involve all sorts of operational demands across a broad area, much of it covered in water. These are issues The War Zone has explored in detail in the past in the context of the military utility of advanced supersonic aircraft using more traditional propulsion options.
It, of course, very much remains to be seen what will ultimately come of the work that GE Aerospace is conducting now. As already noted, the field of work on practical rotating detonation engines of any type is still in its infancy, though significant developments do seem to be occurring at a steadier rate now.
“The successful development, integration, and demonstration of GE’s unique technologies and capabilities will position us to provide differentiating hypersonic propulsion systems for our customers now and well into the future,” Mark Rettig, Vice President & General Manager of Edison Works Business & Technology Development at GE Aerospace, said in a statement in today’s press release. “We have assembled the right expertise, with the right capabilities, and invested strategically to ensure we are aligned very closely with the needs of our customers. The significant results we have had to date give us confidence that we are moving in the right direction.”
We have to also note that there has been major investment over many decades in very high-speed sustained atmopsheric flight in the shadows of classified research and development work. Huge sums have migrated into this area of research in recent years with the rise of hypersonic weaponry, so we don’t know how much of this capability has been explored in that realm if at all.
All told, it will be very interesting to see what else GE Aerospace discloses about this potentially breakthrough propulsion work utilizing rotating detonation combustion going forward.
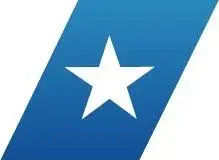