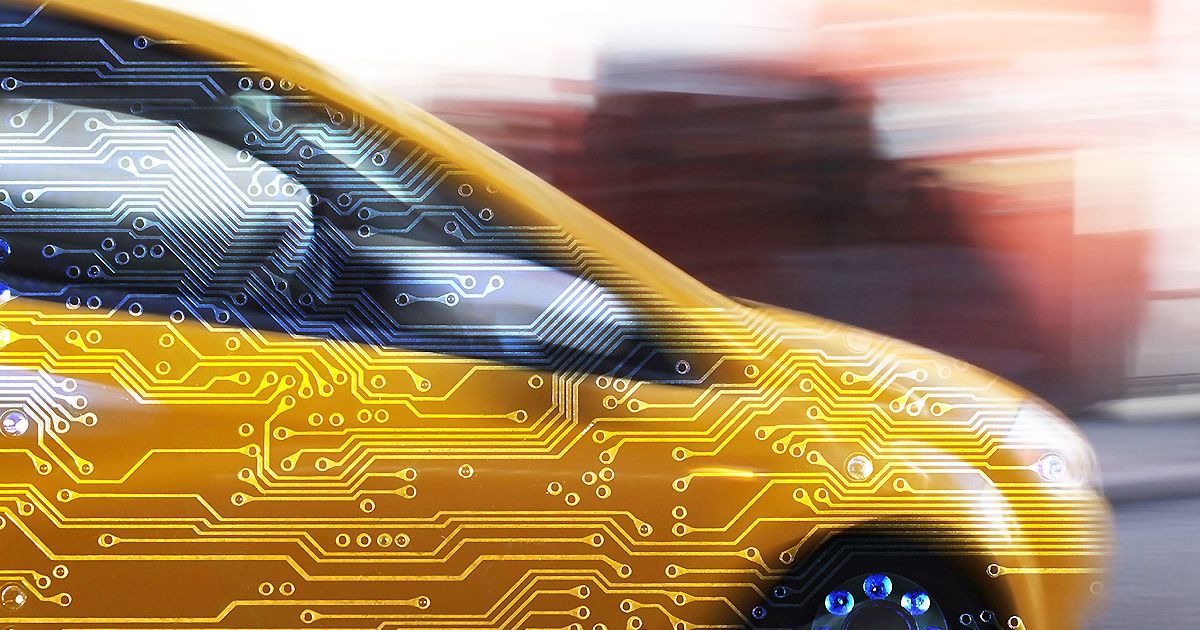
As automakers scramble to create showrooms of new electric and software-driven vehicles, suppliers find themselves racing to develop the parts and systems to make them possible.
Those shorter development cycles could lead to a rise in costly recalls if automakers and their suppliers aren’t careful, said Dan Rustmann, co-chair of Detroit law firm Butzel Long’s global automotive group.
“Historically, when a new vehicle launches, the engineering of all the components takes many years, and there’s significant engineering and validation that goes into every single part,” Rustmann, whose firm represents many suppliers, told Automotive News. “But with compressed timetables, there’s a greater probability we’ll encounter quality issues. And the recall data seems to bear that out.”
Indeed, software is already the industry’s trouble spot. According to data gathered by Ernst & Young, recalls have been costing the industry $40 billion to $50 billion annually in recent years. And more than 40 percent of that is related to software.
As vehicles become more software-driven and connected, and suppliers are asked to speed things up, glitches are sure to pile up higher.
The complexity of today’s environment is “massive,” Dean Phillips, a managing director in Ernst & Young’s advanced manufacturing and mobility practice, told an audience at SAE’s World Congress in Detroit last month.
“We’re suffering the pain of having this fragmented architecture in vehicles with perhaps 100-plus ECUs from different suppliers, developed by different teams with different standards, different protocols and different networking challenges,” he said.
And the challenges extend beyond infotainment displays and other software-driven features.
“If you look at the breakdown on recalls, they really get into the space of the powertrain and the functionally safe domains in the vehicle,” Phillips said.
But the pace is changing now.
Automakers, suppliers and tech companies are spending billions on automotive software development under pressure to accelerate EV development. Last month, the EPA proposed stricter new tailpipe emissions rules that would result in EVs climbing to 67 percent of new light-duty vehicle sales in the 2032 model year.
Last year, Bank of America Merrill Lynch said it expects an average of about 61 new-vehicle models to be launched every year through 2026, a 50 percent jump from the average of the past 20 years. And more complex electric and hybrid models are expected to account for 60 percent of those launches.
“Time is money,” said Jack Cheng, CEO of the MIH Consortium, a Foxconn-led EV development alliance, during an April virtual roundtable with Altair and Lordstown Motors. “At the end of the day, how are you going to be able to hit volumes while Tesla and all the other guys are trying to ramp up? You can feel the threat from a traditional OEM, that they really need to pick up speed.”
Suppliers are already feeling the faster cadence of new-vehicle launches, with program managers juggling more programs than ever, leading to higher costs and delayed timelines. A 2022 study commissioned by the program management solutions company Actify concluded that supplier firms will be working on 2.75 million auto and parts programs in 2025, a steep increase from the already hefty workload of 1.66 million they handled in 2021.
That increase is putting a strain on program managers tasked with coordinating the work and ensuring they hit high quality and durability standards.
The expected rise in quality issues and recalls could be costly for suppliers that are already under financial strain after three years of pandemic and supply chain woes.
Automakers routinely try to pass their recall costs down to the suppliers they hold responsible for them, said Rustmann, who has represented parts companies on matters related to recalls and warranty. That practice could take a greater toll on parts companies going forward in the era of acceleration.
“They’ll negotiate and go back and forth, but suppliers don’t have a whole lot of leverage with the OEMs on any issue,” he said. “So they typically get stuck with pretty large bills from these recalls.”
As a result, he advises, suppliers should double down on their analysis of warranty data so that they can spot potential issues as soon as possible.
They should also be proactive in communicating with automakers when issues arise, though that can prove difficult. Suppliers might be reluctant to bring issues to their customers’ attention because they’re worried they’ll be blamed and charged, while automakers can sometimes be slow in communicating because they first want to build their case for financial recovery from the supplier.
“There are different interests at play,” Rustmann said. “But there’s no question that open and early communication on both sides would help to reduce the frequency and severity of problems.”