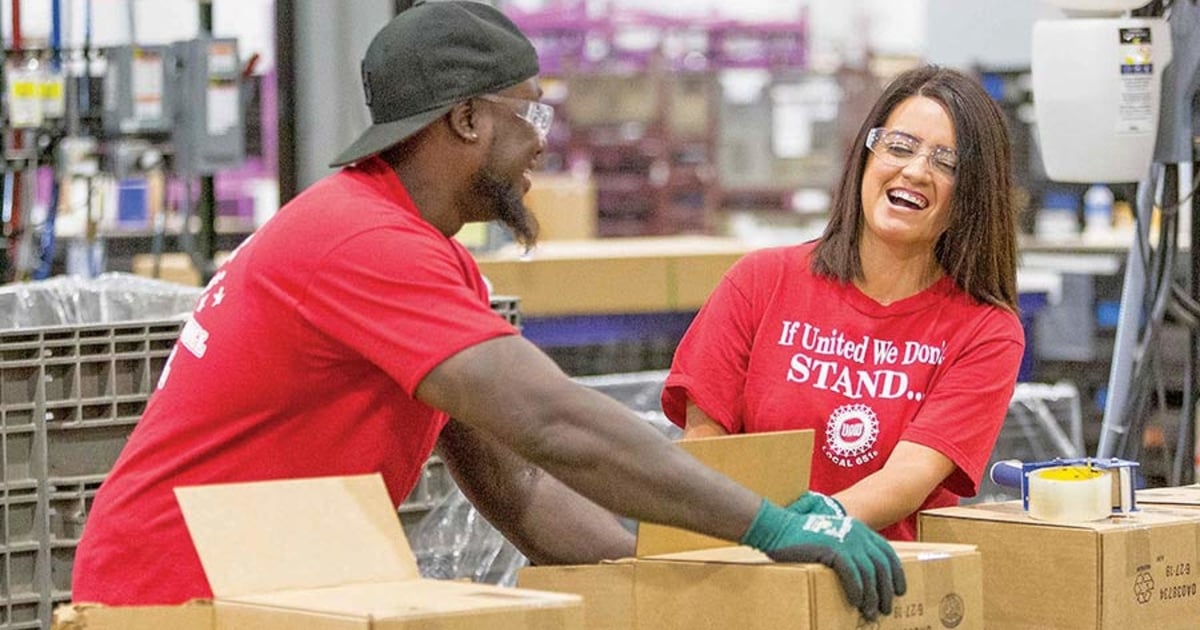
General Motors will invest more than $100 million in its largest parts processing center to add technology, create a more modern warehouse operation and improve worker safety.
The automaker said its Davison Road Processing Center outside Flint, Mich., part of the Customer Care and Aftersales division, will be updated with automated storage and retrieval and mini-load systems, as well as a conveyor system to move parts to employee workstations. Work to install the systems will begin in November, with operations up and running by April 2025.
The facility, which opened in 2019 and employs about 1,460 people, ships roughly 15,000 parts orders daily. It’s the primary distribution site for GM Genuine and ACDelco parts.
GM said the technology updates are intended to help alleviate repetitive strain and improve ergonomics for employees. They come during a growth stage for Customer Care and Aftersales, which has seen double-digit business increases annually since about 2020 that GM expects will continue this year.
“The tools and the technology are here that will allow us to really help people have a better day’s work and be more productive because they’re not slumped over a manual boxing machine or having to move heavy parts throughout the warehouse,” John Roth, GM’s global vice president of Customer Care and Aftersales, told Automotive News. “It does help us also capitalize on improving our process and the overall efficiency, so you get a much better customer experience that way as well.”
The automated storage and retrieval system, for instance, will reduce employee lifting and speed the fulfillment process by storing up to 46,000 pallets containing processed parts to be sent to other distribution centers.
An automated mini-load system can store up to 146,000 parts for shipment and can sort and bring smaller parts to employees. A separate conveyance system will move parts to workstations along 3.5 miles of track, minimizing the need for walking and lifting.
“It’s an important investment,” Roth said. “It all starts with enhancing the safety, preparing for that growth, and by preparing, you’ve got to modernize and take advantage of the new technology that exists in the marketplace.”
This funding follows a $20.5 million investment in three Customer Care and Aftersales facilities in January, including the Davison Road location, which received $3.5 million to add automatic boxing machines for parts. Parts centers in Memphis, Tenn., and Ypsilanti, Mich., also received technology upgrades.