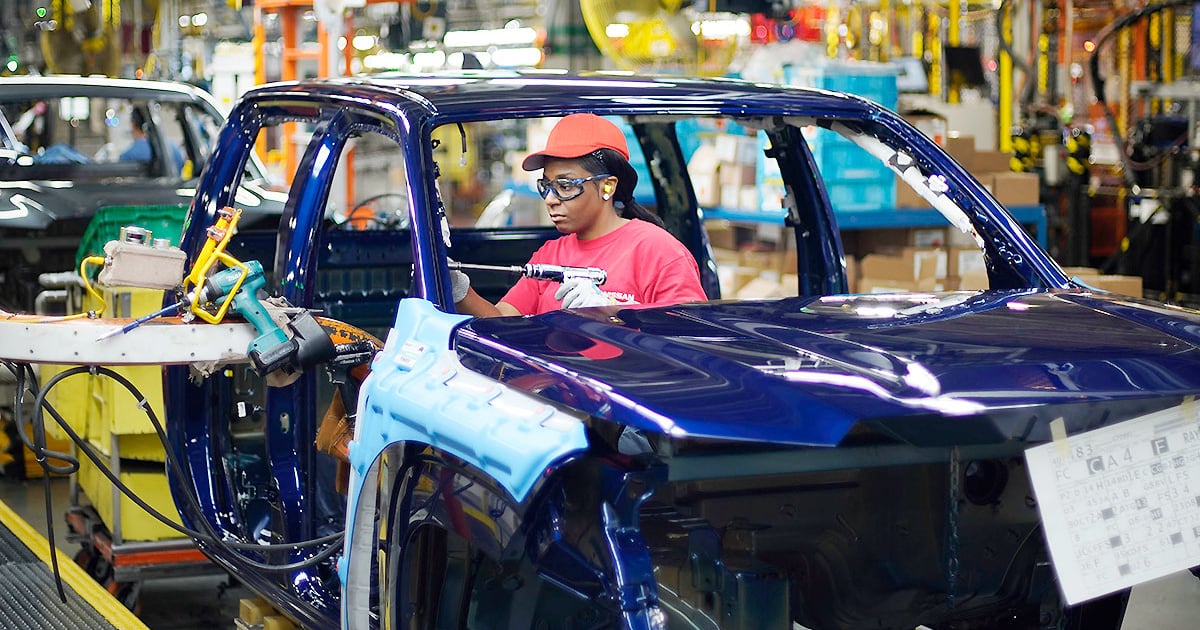
Nissan Motor Co.’s Canton, Miss., factory has stamped out more than 5 million gasoline-powered trucks, crossovers and vans since the first vehicle — a Quest minivan — rolled off the assembly line in spring 2003.
Two decades later, the Japanese automaker is transforming the 4.7 million-square-foot industrial operation for the electric age.
Canton’s metamorphosis rests on the shoulders of David Johnson, Nissan North America’s production and engineering boss who once aspired to be a space explorer.
The 47-year-old steers a $500 million effort to remake the assembly plant into a cornerstone of electric vehicle production in North America. Mid-decade production begins on the first of several battery-powered models for the Nissan and Infiniti brands.
“Canton will be North America’s electrification hub for the next five to six years,” Johnson told Automotive News last week.
“That’s where we’re going to bring in the new platforms, the new technology,” he said.
This is not Nissan’s first rodeo in building EVs. The automaker pioneered the segment more than a decade ago when it launched the Leaf hatchback. It was also two years before Tesla showed up and redefined the electric vehicle from an underpowered compliance vehicle to a performance daily driver with the Model S sedan.
Nissan is vowing to take the lessons learned from its first act and apply them to the second, which the company said will include a wave of competitively specced and designed battery models.
“They’re all new platforms, new technology, and more connectivity,” Johnson said.
But the manufacturing game plan will be the same.
“You adjust to the technology first, and then you figure out how to adjust everyone in the facility to that new technology, whether it’s product technology … or the manufacturing technology that comes with the vehicles,” Johnson said. “The Canton project is big, but it’s not overwhelming because we got a great team.”
Nissan will build EVs alongside the gasoline-powered Altima sedan on one of Canton’s two assembly lines.
According to a supplier production schedule, assembly on a pair of electric sedans will begin in 2026. A couple of battery-powered crossovers will follow in 2027 and 2028.
Nissan won’t lack room to grow at Canton, which is operating at a little more than half its annual capacity of 410,000, AutoForecast Solutions estimated.
The output of the low-volume Titan pickup on the factory’s other assembly line, which it shares with the Frontier midsize pickup, ends next year as Nissan exits the Detroit-dominated large-truck segment in which it failed to make a dent. Production of the Frontier, last redesigned in 2021, could extend into 2027, according to the supplier.
Johnson declined to say when Canton production might go all-electric. “All new product … that I’ve got visibility to right now in the Canton plant is EV,” he said.
At Canton, Nissan seeks to produce fewer emissions in building its zero-emission vehicles as the automaker strives to reach carbon neutrality globally by 2050.
The path to getting there is building vehicles in a more energy-efficient manner.
“How do we reduce our overall electricity consumption in the factory?” Johnson said. “How do we reduce our reliance on compressed air and natural gas?”
Upgrading the plant for EV production creates an opportunity to install newer energy-sipping machinery. “We want to ensure it takes less energy to build the next model versus the last,” Johnson said.
Pivoting the factory to battery vehicles is a complex endeavor.
Nissan must expand the facility’s physical footprint to accommodate the assembly of battery packs and other components.
“We will drive for more localization to reduce CO2 emissions in the supply chain,” Johnson said.
New technologies, such as laser brazing, will be introduced in the body shop to create parts that are “unique to the styling of our vehicles,” Johnson said. “We’re going to modify our onsite presses for full aluminum capability,” he said.
The assembly line will require modification rather than a rip-out.
The heaviest changes will be in trim and chassis, where Nissan will deploy the simultaneous underbody mounting system to mate the chassis to the battery powertrain.
The new vehicle platforms will bring greater automation. Nissan said about 20 percent of trim and chassis work on the EV line is automated compared with 6 to 10 percent on the combustion engine line.
But robots won’t come at the expense of humans. New positions in battery pack assembly and other production areas will offset jobs lost to automation in trim and chassis.
“We’re just maintaining and upskilling the jobs,” Johnson said. “People may move around, but overall headcount is basically flat.”
Integrating EV production without affecting current output will be a challenge.
“Anytime we bring in new technology, [the] material and process flow is going to be different than before,” Johnson said. “You have to work around current operations and processes to keep the vehicles you’re building today flowing while preparing for the future.”
Johnson said his message to the team is to prioritize the EV line.
“It’s OK to be a little bit suboptimal in the last months of a particular vehicle or project’s life to [ensure] that we’re fully optimizing for the start of the next,” he said. “You can’t shortchange the future while continuing to work on today.”
Planning for EV production at Canton began before Thanksgiving last year.
The assembly line equipment won’t arrive until next year. But the arduous work force upskilling is underway. Nissan expects to retrain the 2,000 production employees on Canton’s Line 2 affected by electrification.
“I am a huge believer in the capability of people,” Johnson said, noting that the work force has proven to adapt and change over many years of new models and assembly techniques.
Work force retraining begins with Nissan dispatching Canton’s most experienced engineers and technicians to Japan, where they learn new vehicle technologies and manufacturing techniques at the company’s Atsugi technical center and Tochigi assembly plant.
Meanwhile, virtual reality technology and high-powered software give Nissan engineers a head start in planning the production line and workflow, helping prevent production delays.
“We’ve got training folks working in virtual reality [to understand] where we may need to make additional changes that we wouldn’t recognize probably until much later in the design and development cycle,” Johnson said.
Next year, workers will move from the virtual world to the real one when EV production equipment gets installed.
“Before we get into production trials in late 2025 or early 2026, the technicians will be very familiar with that product before the first real vehicle even goes down the line,” Johnson said. “So we can deliver quality and consistency from job one versus building it up over time.”