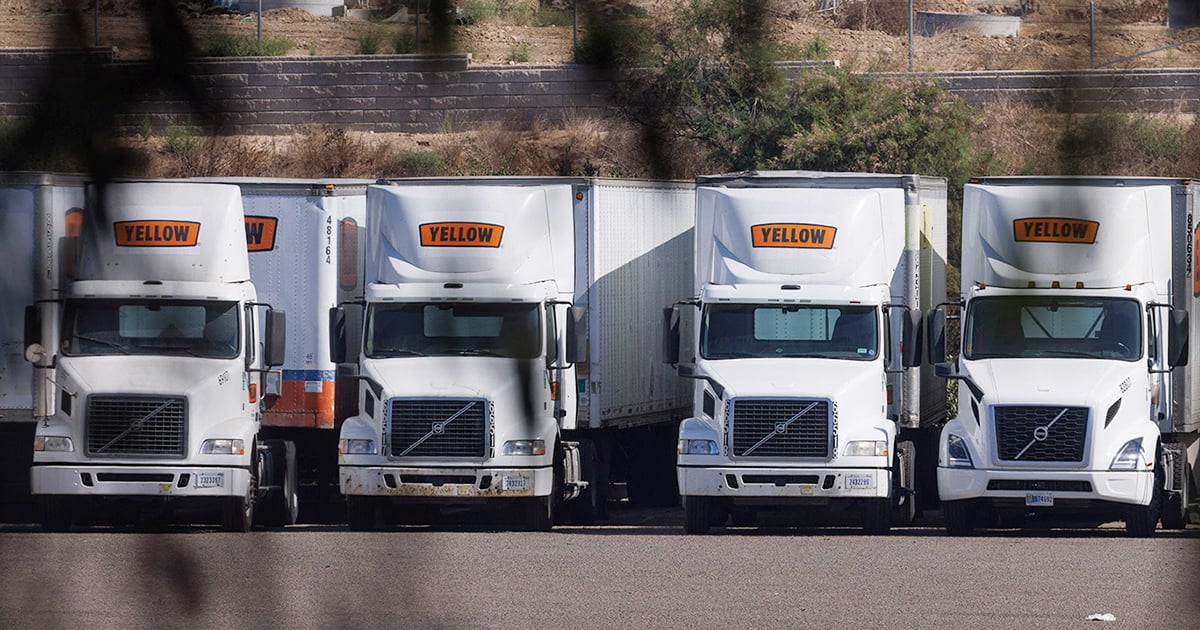
Last week’s bankruptcy of one of the largest trucking companies in the U.S. serves as a reminder to suppliers of the still-fragile state of the supply chain, industry experts said.
Trucking company Yellow Corp., a once-dominant player in the “less-than truckload” segment that hauls cargo for multiple customers on a single truck, filed for Chapter 11 bankruptcy protection and laid off 30,000 workers Aug. 7, about a week after it had halted operations. Yellow, whose customers included major retailers and manufacturers, had a market share of 8 to 10 percent, according to brokerage TD Cowen.
“I think the Yellow bankruptcy is going to have more of an impact than we think, and I don’t believe we’ve fully seen it yet,” said Laurie Harbour, CEO of Harbour Results Inc., which advises tool and die companies and other manufacturers.
The bankruptcy comes as the auto industry continues to sort through various supply chain issues. While many of the problems that have dogged auto manufacturers in recent years, including the microchip shortage, have eased in recent months, transportation issues have been singled out by some supply chain experts as an issue to keep an eye on moving forward.
The concern is not a new one. Since the start of the COVID-19 pandemic, automakers and suppliers have dealt with higher costs for logistics and shipping, whether by rail, truck, boat or plane, to the tune of as much as 30 to 40 percent increases when compared with before the pandemic, Harbour said.
Increased transportation costs and greater logistics uncertainty are among the factors that have contributed to the heightened financial pressure many suppliers have faced in recent years.
“All of those factors sort of get netted into the ask by suppliers with their customers” when seeking financial relief, said Michael Robinet, executive director of Automotive Advisory Services at S&P Global Mobility.
To be sure, the impact of Yellow’s bankruptcy on the auto industry is uncertain. It could be quite limited, said Dan Hearsch, managing director at AlixPartners.
“I suspect that there are some blips that are specific to models or maybe something to do with a particular carrier,” he said, referring to broader transportation concerns. “But otherwise, we’re not hearing much disruption on things getting moved around.”
Still, suppliers have been rattled by heightened uncertainty in recent years, Harbour said. Shortages of truck drivers and rail cars and backups at ports have all forced parts makers and tool and die companies to re-examine their supply chains, she said.
“In some regards, you think logistics is just sort of a given, that you’d be able to find someone to move something,” she said. “That should be easy, but it’s not so much the case.”
Premium freight became a “massive problem” for suppliers and automakers during the early parts of the pandemic, especially as supply disruptions such as the microchip shortage made production schedules less reliable, Robinet said.
“Those costs have come down, but that’s something suppliers have had to deal with,” he said.
How much of a dent logistics issues have made to any given supplier’s bottom line depends in large part on its physical footprint.
“For some, logistics are a small portion of their total costs, but for others whose components are larger or they have subsystems coming from Mexico or other lower-cost locations, logistics could be a higher cost,” Robinet said.
Those costs could be a factor in suppliers re-examining their manufacturing footprints and their supply chains, Harbour said.
“This is going to drive a lot of discussion about where you’re located as a supplier in relation to an assembly plant,” she said. “If I’m across the street, that’s different than if I’m 100 miles away or 1,000 miles away.”
One way to reduce shipping expenses over the long run would be to source more components locally or to ship parts to automakers over shorter distances.
Many companies are already revamping their supply chains as electrification ramps up, given new federal incentives and heightened geopolitical tensions making the prospect of shipping parts or vehicles around the globe less appealing in some cases. Continued concerns around transportation and logistics could only serve to further incentivize companies to regionalize their supply chains.
“This is an issue that’s everywhere,” Harbour said. “It’s maybe not impacting the industry as bad as semiconductors, but it certainly has the potential to be [that bad] as we continue to have growing demand.”
Reuters contributed to this report.