Heavy EV batteries grab headlines, but traditional electric motors aren’t exactly light either. Enter axial flux.
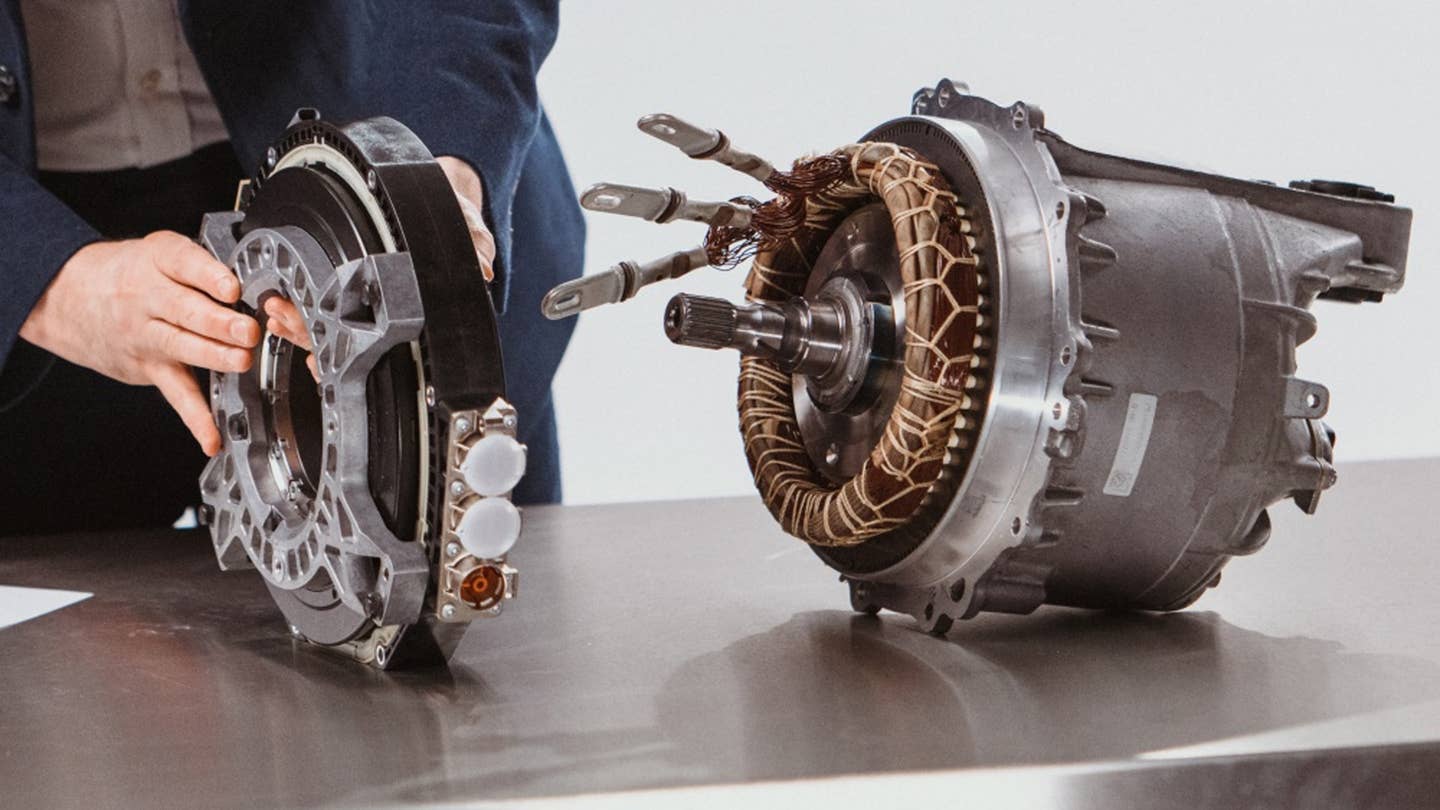
Electric vehicles are heavy, but have you heard they’re fast, too? Automakers are barking up the wrong tree when it comes to what enthusiasts want. Lightweight electric roadsters and sports cars just aren’t being sold right now, and while heavy batteries are largely to blame, that’s far from the whole story. We can solve a lot of these problems before lithium-ion goes on a diet.
It’s going to start with things like electric motors. Today’s EVs are almost entirely powered by radial flux machines. They’re efficient and relatively easy to produce, but by nature of how they work, they need to be relatively long and barrell-shaped in order to put out enough power for a car. By contrast, axial flux motors can be smaller and flatter like a frisbee but still exhibit the same potential. This is because of the way their magnets are arranged. Magnetic force—or flux—in axial motors travels parallel to the axis of the motor rotation instead of perpendicular, or radially. This means they can take a different form.
YASA
The problem has been that they’re much tougher to build at scale, which has prevented their widespread adoption in EVs. Because of one company’s efforts, though, the concept looks finally ready to spread its wings.
As with other EV technology, axial flux motors aren’t exactly a new idea; the idea was already taking shape at the hands of Michael Faraday in the early 1800s. However, you can largely thank one man for the auto industry’s renewed interest: Dr. Tim Woolmer. Dr. Woolmer’s been obsessed with the concept since writing his Ph.D. thesis nearly 20 years ago, and his research led to the birth of what’s known as the Yokeless and Segmented Armature axial flux motor. He founded a company called YASA in 2009 to continue development, inking a number of deals with automakers to supply YASA motors for EVs before being acquired by Mercedes-Benz in 2021.
YASA
His journey started with a simple question: “Why are there no electric cars?” The obvious constraint in the 2000s was battery tech, but today, that’s no longer the main obstacle. To really be efficient and lightweight, EVs must be reconsidered as entire systems from the ground up, and Dr. Woolmer has figured out a key piece of the puzzle. His company’s technology, in many ways, holds the key to an electric sports car you might actually want to buy.
Cutting Mass
You might wonder why Dr. Woolmer decided to research electric motor design if the existing radial flux units in almost all EVs are very efficient. After all, he tells me “I would’ve been happy working on batteries, chargers, anything I found interesting.” The idea of “mass decompounding” is really what drove him towards axial flux designs, though. At least on paper, the new configuration promised a 30% reduction in size as compared to a radial flux of similar output, as well as considerable weight savings. That percentage is far more significant than you might think, especially in dual- or tri-motor EVs. “If we can take 100-200 kilograms [220-440 pounds] out, you’re starting to really influence your vehicle.”
And not just from a powertrain perspective, but in terms of mass and packaging overall. If a considerable amount of weight and volume can be saved when it comes to components like a motor, it effectively means everything that supports it can be lighter and more compact. As a system, the car can get much more efficient. Forget a bigger battery—the battery you have will be able to take you much further. We haven’t really seen this practice taken to extremes in this direction yet, but we have certainly seen the opposite. I’m of course talking about the 9,000-pound Hummer EV.
YASA
How much of a difference could this really make, though? Dr. Woolmer tells me that his company has “traction motors that will power a normal-sized car that can be five or six kilograms.” Imagine if your sports car’s engine was 13 pounds. Getting there was quite the journey.
The Trouble With Axial
The axial flux motor is very nice conceptually, but it’s more difficult to mass-produce compared to radial flux. Furthermore, there are many configurations of axial flux motors, so Dr. Woolmer had to narrow down which was best to develop at scale.
He landed on the YASA configuration in the late 2000s after becoming interested in a material called soft magnetic composite, commonly referred to as SMC. “Instead of stacking laminations… you can press it into a three-dimensional shape with quite simple tooling.” That has a lot of advantages in terms of motor construction and efficiency, but “There’s one limitation, which is you can only make parts which are—maximum—the size of your hand.” This is due to the immense pressure needed to compact SMC into a solid form.
The limitation ultimately led to segmenting the stator, the stationary part of the motor which contains the copper windings. This had a waterfall effect in terms of manufacturability, efficiency, and torque density. He didn’t know then, but he just built a future for the technology. Now that he’d figured that out—he made it all sound so simple—he just needed to find investors for his design in 2009, when no mass-market EVs were on the road. Likewise, the tooling to create these advanced motors did not exist. “We’ve had to design a lot of machines that make the machines,” Dr. Woolmer explained, adding that 70% of the tooling currently used to build the company’s motors was custom built by YASA.
Gathering Believers
As you might expect, Dr. Woolmer was met with a lot of skepticism. He says early investor talks went something like this: “There are no electric cars. There’s no market for your product. Even if there was a market, and even if you started selling your technology, you’re just gonna lose money, and it’s going to be a disaster.”
This didn’t discourage YASA enough to stop. Soon after its founding, it got its first big break to build motors for the Jaguar C-X75 concept in 2010. The unorthodox turbine-powered hybrid-electric supercar never made it into production, though it did make a splash in the 2015 James Bond film Spectre. Next, it supplied YASA motors for the $2 million Koenigsegg Regera plug-in hybrid supercar in 2015, the first production vehicle to feature its tech. Then came orders from Ferrari and McLaren before the company was bought by Mercedes, though it’s still working with outside partners.
Jaguar
Still, in 2023 there are still no mass-market axial flux EVs on the market. Why? Well, many automakers are just getting their very first electric offerings on sale, which all started development before YASA’s work was really out there. Also, axial flux motors are great for packaging between an engine and a transmission on account of their flat profile, so high-performance hybrids seemed like a natural starting place for manufacturers to test out the technology.
The real opportunity in the pure EV space has yet to be realized, but Dr. Woolmer says it’s just a matter of time. More than anyone else in the auto industry I’ve spoken to (on the record) about the future of enthusiast cars, he understands that it’s not just about how fast you can get to 60 miles per hour. “There’s been a bit of a baselining, everyone making a fast EV,” he told me. That’s turned out to be pretty easy to do. We can see a number of quick, heavy machines from the likes of Tesla, General Motors, and more. But now “the mindset has changed. Everyone has recognized they’re fast. Now the next change is how to make them more engaging, how to make them more fun.”
Not Just Fast
To do so will require cutting weight back into the realm of sanity and using energy more efficiently as opposed to simply stuffing more battery cells into a car. That’s exactly what axial flux motor tech allows. “As batteries improve and the architectures get optimized and the weight of the subcomponents comes down, there’s no reason why they can’t actually be lighter than ICE engine cars,” Dr. Woolmer tells me.
All of this has led to YASA’s upcoming generation of axial flux motors, currently in development and set to take the stage this decade. These motors are “going to be pushing more than 30 kW [40 hp] per kilogram.” The implications are almost unbelievable. A 300-horsepower weekend runabout could be powered by a motor weighing less than the average watermelon.
Dr. Tim Woolmer holding a stator coil from one of the company’s next-generation electric motors. YASA
More than anything, this will allow for EVs to drive and feel different than they do today, even if batteries are still heavier than most would like. “[The OEMs] are struggling to find differentiation with electric cars, more so when they had petrol and diesel cars.” A novel technology like YASA specializes in is going to be key to carving out a niche and delivering a distinct driving experience.
I share Dr. Woolmer’s sentiment that we really are just at the beginning of this journey. The ideal electric motor configuration hasn’t even been settled. Combustion cars have had the better part of 100 years to develop, and we can’t expect EVs to do everything better right off the bat. The promise is evident, though. By the time YASA’s next generation of motors arrive, the batteries, power electronics, and more will have improved as well. Skepticism is warranted, but technology that’s practically already here is ready to kick the door down on a new generation of cheap, lightweight, and simple sports cars. Don’t just take my word for it, take Dr. Woolmer’s.
Got a tip or question for the author? You can reach them here: peter@thedrive.com