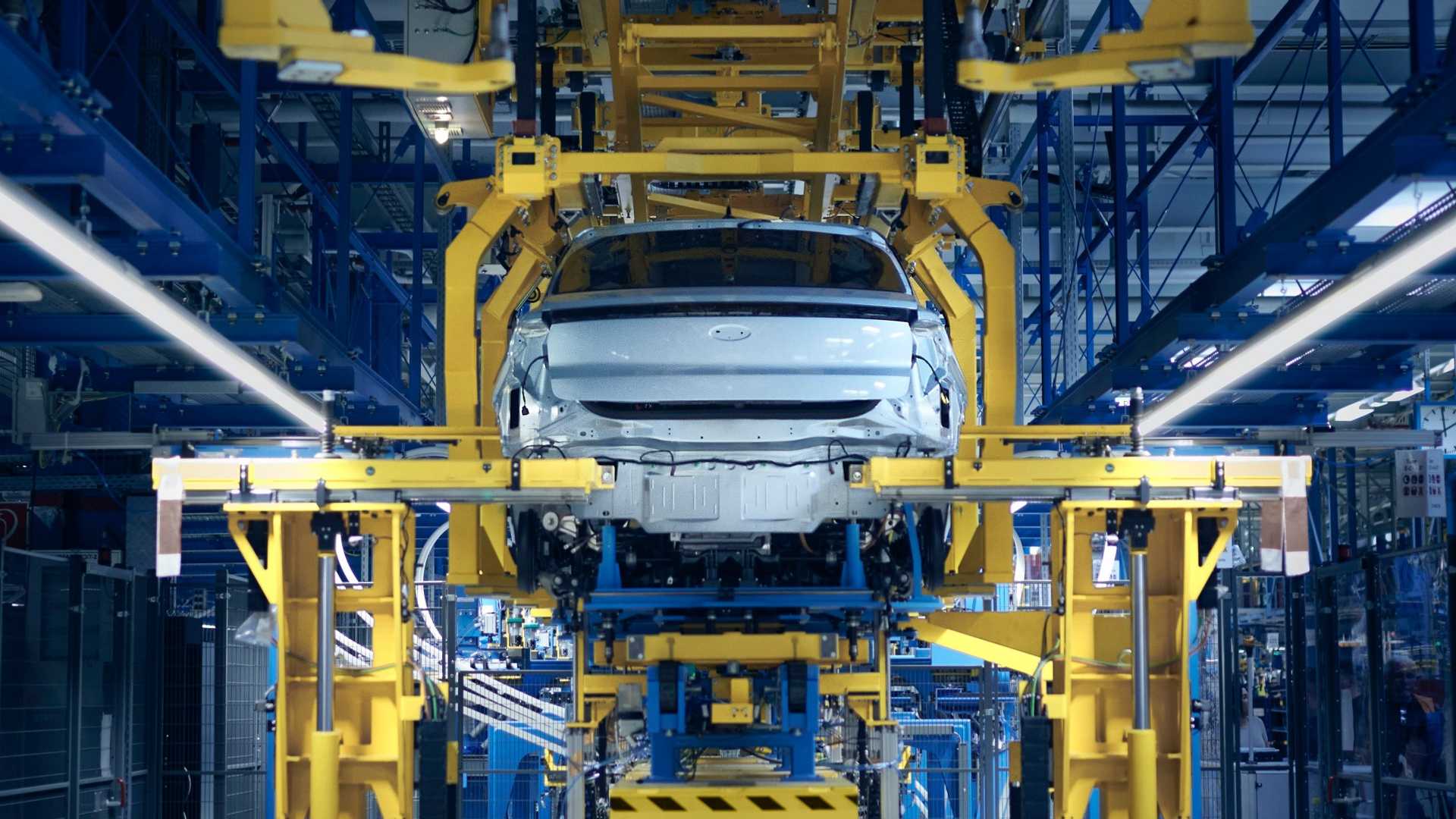
As automakers race to make electric vehicles more affordable—both for them to build and for customers to buy—Ford made a splash on Tuesday when its CEO, Jim Farley, revealed during an earnings call that a secretive “skunkworks” team had been working on a low-cost EV platform for the past two years.
The opportunity there is clear. Building EVs cheaply and profitably has been a hard nut to crack for most of the auto world (outside of China, at least). The typically high upfront cost of today’s EVs is keeping eager buyers from pulling the trigger. Ford needs to cut costs to make its EV business profitable. But why did the Detroit carmaker rely on a small group separate from the “mothership,” as Farley put it?
Get Fully Charged
EVs still aren’t profitable for most automakers
Ford’s EV business lost $4.7 billion last year. Next-generation electric models that are cheaper to build will be crucial to the company’s long-term success.
One answer: That startup-like approach gives it an edge against Tesla.
Tesla and other newcomers aren’t encumbered by a century’s worth of “this is the way we do things,” like legacy automakers are. That’s allowed them to rethink how cars are built from the ground up. And Ford is smart to emulate that clean-slate approach here, said Sam Fiorani, the Vice President of Global Forecasting at AutoForecast Solutions.
“In cases like this, where it’s something that needs a radical relook of the processes, working with a team outside of the norm fits that perfectly,” Fiorani told InsideEVs. “The legacy companies need more of that today to narrow the gap with them and the new EV players.”
Although EVs already feel like a mainstay of the car business, the reality is that most automakers haven’t been seriously working on them for all that long. After spending decades fine-tuning the process of assembling gas vehicles, old-school automakers like Ford are still very much figuring out how to build EVs efficiently and profitably.
It’s a whole new world out there with new types of components, new supply chains to navigate and new constraints to dal with. All that lends itself nicely to a ground-up strategy where you tell a small team, “Here’s a whiteboard. Fill it,” Fiorani said.
“When you’re starting with EVs, not only are you starting with a dedicated platform and a new powertrain, but potentially a new way of assembling the vehicles,” he said. Plus, relying on a small group can help an automaker keep buzzy new efforts on the down low, which Ford apparently managed to accomplish.
Tesla is set to start production of its own cheaper-to-build, next-generation vehicle platform in 2025. Tesla CEO Elon Musk has said that technology will cut manufacturing costs in half and debut a groundbreaking new way of assembling cars.
Sure, the EV-maker’s head honcho is prone to exaggeration, but this isn’t coming out of nowhere.
Tesla has already achieved some of the fattest margins in the car business, in part by pioneering manufacturing processes that the old guard is beginning to adopt. For example, Tesla uses “Gigacasting” to produce large sections of its cars’ bodies out of single pieces of aluminum, drastically cutting down the number of parts needed for a car’s basic structure. Now that’s catching on at giants like Toyota.
Farley made clear that Musk’s mysterious, upcoming car is a big reason it’s focused on cutting manufacturing costs, telling investors on Tuesday: “The ultimate competition is going to be the affordable Tesla and the Chinese OEMs.”
Ford has used small, secretive teams to develop vehicles before; that’s included projects like the Mustang GTD race car. But creating a startup atmosphere makes even more sense when that’s the fundamental nature of your biggest competitor. And this vehicle isn’t just some limited-production project for competition.
Farley said the team has developed a flexible platform that will underpin several different vehicles. We don’t yet know what those vehicles are or when they’ll hit the market. What’s clear is they’ll be incredibly important to Ford’s electric future.
Do you work for Ford and have something interesting to share? Contact the author: tim.levin@insideevs.com